Discharge System
Maximal throughput while minimizing back flow
Our wear-resistant, rubber-covered or cast dischargers come in two general designs – radial and curved. Solutions that suit both trunnion overflow and grate discharge mills are made of light- weight rubber parts or heavy-duty steel parts or combinations of both, depending on customer objectives. The latest innovations, like Megaliner and Spiral Turbo Pulp Lifter, increase efficiency.
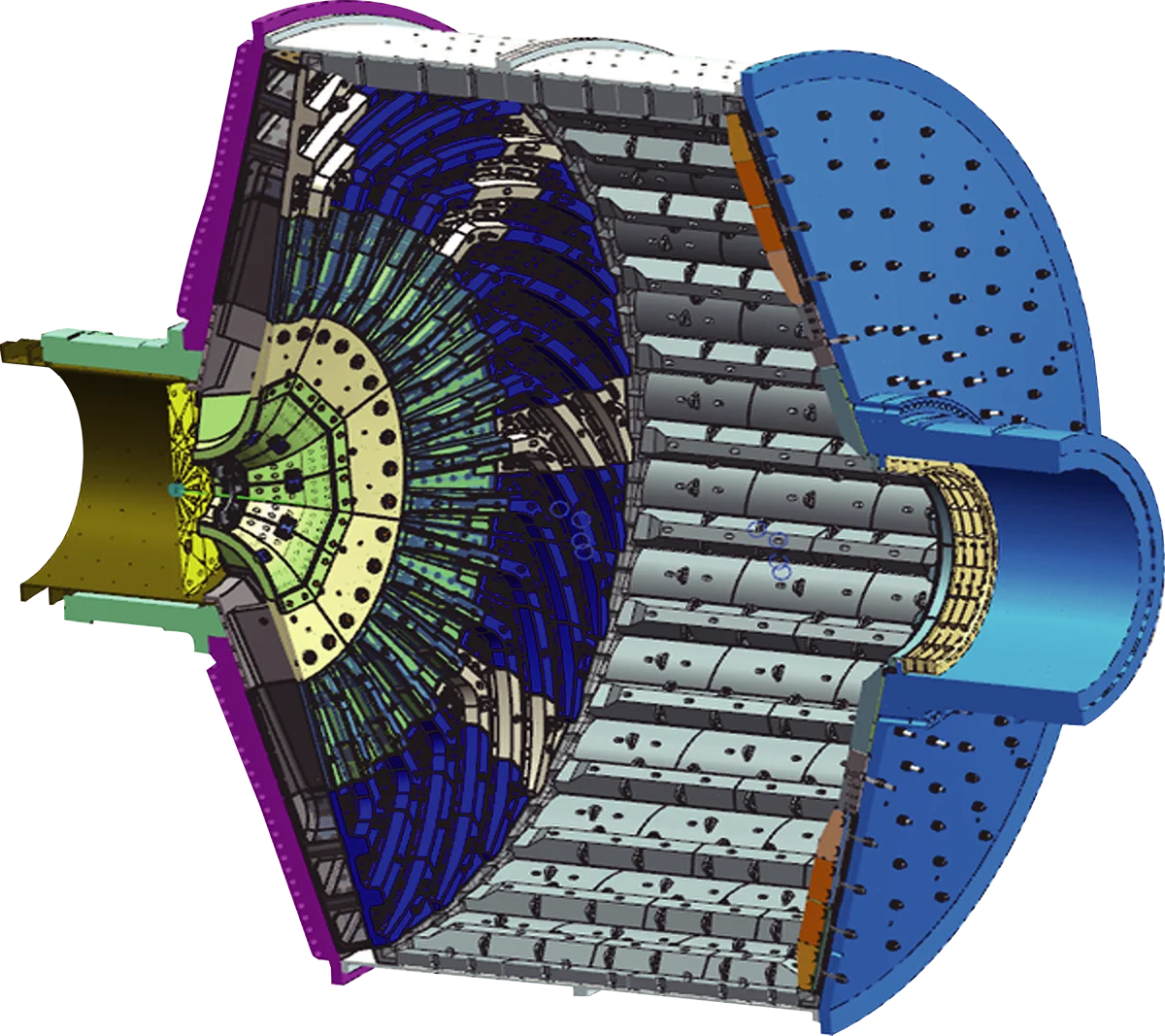
Shell Liner
Long wear life and balanced design to maximize mill availability.
The shell liner has a major influence on grinding efficiency. It transforms the mill rotation into charge motion, and both profile and spacing must be selected to suit each specific mill. When designing a shell linerliner, the type of ore, mill size and speed, maintenance schedules, safety,impact levels and efficient use of materials should all be considered.
Feed end Liner
A balanced feed head liner design minimizes downtime
The feed-head liner is designed with consideration to the shell liner
design. All components must be in balance to minimize the number of maintenance stops. The number of individual parts is kept to a minimum for easy istallation. A wide selection of optimized profiles and the possibility to mix all different types of liner materials gives you additional flexibility.